m92 suervo motor instruction manual
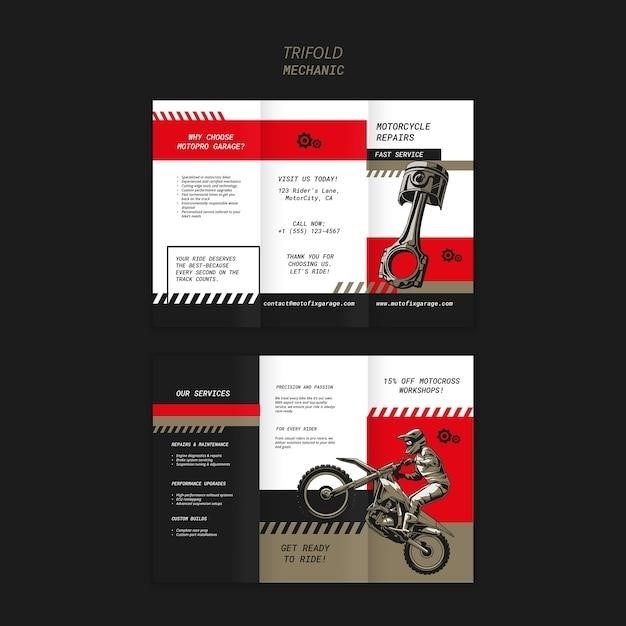
M92 Servo Motor⁚ A Comprehensive Overview
This manual provides essential guidance for the M92 servo motor. It covers installation‚ operation‚ maintenance‚ and safety. The M92 is a compact‚ high-performance servo motor ideal for various applications. Detailed instructions ensure safe and efficient use. Consult this manual for troubleshooting and optimal performance.
Understanding Servo Motors and their Applications
Servo motors are electromechanical devices that provide precise control over angular position‚ velocity‚ and acceleration. Unlike standard DC motors‚ servo motors incorporate closed-loop feedback mechanisms‚ typically using a potentiometer or encoder to monitor their actual position and compare it to the desired position. This feedback allows for accurate positioning and precise control‚ even under varying loads. They are widely used in various applications such as robotics‚ automation‚ industrial machinery‚ and model aircraft. In robotics‚ servo motors enable precise movements of robotic arms and manipulators‚ while in automation‚ they control the positioning of components in assembly lines. Industrial machinery relies on servo motors for accurate and repeatable movements in processes such as cutting‚ welding‚ and packaging. In model aircraft‚ they control the movements of flight surfaces‚ enabling precise maneuvering and control.
The versatility of servo motors stems from their ability to operate with various control signals‚ including pulse width modulation (PWM)‚ enabling precise control of their rotation angle. Their high-precision capabilities and robust construction make them reliable and efficient actuators in a wide array of applications. The choice of a specific servo motor often depends on factors such as required torque‚ speed‚ size‚ and operating voltage.
The M92 Servo Motor⁚ Key Features and Specifications
While specific details for the M92 servo motor are limited in the provided text‚ we can infer key features and specifications based on similar models and general servo motor characteristics. The M92 is described as a compact‚ high-torque AC servomotor with a 450W output‚ suggesting it’s designed for demanding applications requiring high power and precision. Its compact design likely prioritizes space efficiency‚ making it suitable for integration into smaller systems. The high torque capability indicates a strong ability to overcome resistance and maintain accurate positioning under load. The 450W power output suggests a robust motor capable of handling significant work demands.
Expect the M92 to have a specific operating voltage range‚ stall torque rating (indicating the maximum torque before stalling)‚ and speed characteristics. It will likely use a standard control interface‚ possibly pulse width modulation (PWM)‚ for precise control of its rotational position. Additional specifications such as weight‚ dimensions‚ and mounting configurations would be detailed in a full product datasheet or manual. The absence of a readily available specification sheet online emphasizes the importance of consulting the official documentation for complete information. Remember to always refer to the manufacturer’s specifications for the most accurate and up-to-date details.
M92 Servo Motor Installation⁚ A Step-by-Step Guide
Precise installation instructions for the M92 servo motor are unavailable in the provided text. However‚ a general guide for installing similar servo motors can be outlined. Begin by carefully reviewing the motor’s specifications and diagrams to understand its mounting points and connection requirements. Securely mount the M92 to its intended location‚ ensuring stability and proper alignment. Use appropriate fasteners and torque specifications to avoid damage. Connect the power supply cables‚ adhering to the polarity markings (+ and -) to prevent damage or malfunction. Incorrect polarity can lead to immediate motor failure.
Next‚ connect the control signal wires according to the pinout diagram. These usually consist of power‚ ground‚ and a control signal line (often PWM). Ensure secure connections to avoid intermittent signals or shorts. After connecting the wires‚ carefully inspect all connections for any loose wires or potential issues. A visual inspection will help to prevent errors before powering the system. Finally‚ test the motor’s operation using a suitable control system and verify its movement and response. Always refer to the manufacturer’s documentation for the specific installation procedure and safety precautions for the M92 servo motor.
Operating the M92 Servo Motor
This section details the M92 servo motor’s operation. Proper connection to power and control systems is crucial. Programming and control methods vary depending on the application. Always follow safety guidelines for optimal performance and longevity;
Connecting the M92 to Power and Control Systems
Connecting the M92 servo motor to your power and control systems requires careful attention to detail to ensure proper functionality and prevent damage. First‚ verify the M92’s voltage requirements; this information should be clearly specified in the motor’s datasheet or accompanying documentation. Failure to supply the correct voltage can lead to malfunction or permanent damage. The power supply should be capable of providing sufficient current to meet the motor’s operational demands‚ taking into account peak current requirements during high-load situations. Insufficient power can lead to erratic behavior or failure to operate correctly.
Next‚ connect the motor’s power leads to the appropriately rated power supply terminals‚ observing polarity (+ and -). Incorrect polarity can result in immediate damage to the motor. For control signals‚ refer to the M92’s specifications and the documentation for your control system. Most servo motors use Pulse Width Modulation (PWM) signals for control‚ and the frequency and pulse width determine the motor’s position and speed. The signal wire should be connected to the designated control input on the servo motor. Always double-check all connections before powering up the system. A faulty connection can cause unexpected behavior or damage. Consult the M92’s technical documentation for a detailed wiring diagram and connection instructions specific to your setup.
Programming and Control of the M92 Servo Motor
Controlling the M92 servo motor typically involves sending Pulse Width Modulation (PWM) signals. The PWM signal’s pulse width dictates the motor’s angular position. A longer pulse width corresponds to a greater angle‚ while a shorter pulse width results in a smaller angle. The frequency of the PWM signal is usually fixed‚ often around 50 Hz. Programming the control involves generating these PWM signals with the correct pulse width to achieve the desired motor position. Many microcontroller platforms‚ such as Arduino‚ provide libraries that simplify this process‚ offering functions for generating PWM signals to control servo motors directly.
To program the M92’s movements‚ you’ll need to use a suitable programming environment and language. The specific code will depend on your chosen platform and control system. However‚ generally‚ you’ll need to specify the desired angle (in degrees) and the motor will automatically adjust its position accordingly. Calibration might be necessary to accurately map the PWM pulse width to the motor’s physical angle. Furthermore‚ error handling and safety checks should be incorporated into your code to manage potential issues and prevent unexpected behavior. This includes monitoring the motor’s current draw and implementing protective measures to avoid overloading or overheating.
Troubleshooting and Maintenance
This section details common M92 servo motor problems and their solutions‚ ensuring optimal performance. Regular maintenance‚ including cleaning and lubrication‚ is crucial for extending its lifespan. Consult this guide for resolving issues and maximizing motor efficiency.
Common Issues and Solutions for the M92 Servo Motor
This section addresses frequently encountered problems with the M92 servo motor and provides practical solutions for resolving them. One common issue is erratic movement or failure to respond to control signals. This often stems from loose connections‚ power supply irregularities‚ or a faulty control signal. Check all wiring and connections carefully‚ ensuring secure seating and proper polarity. Verify the power supply voltage meets the M92’s specifications. Examine the control signal for any inconsistencies or noise that might interfere with proper operation. A malfunctioning control circuit could also be the culprit‚ requiring more in-depth troubleshooting.
Another potential problem is excessive noise or unusual sounds during operation. This might indicate excessive friction within the gear train‚ possibly due to wear or debris. Inspect the gears for damage and clean any accumulated dirt or debris. If necessary‚ apply a small amount of appropriate lubricant to reduce friction and noise. Overheating can also be a symptom of excessive load or internal problems. Ensure the motor is not overloaded beyond its capacity and the surrounding environment allows for adequate heat dissipation. If the motor consistently overheats‚ despite these checks‚ it may require professional servicing or replacement.
Finally‚ intermittent operation or complete failure can indicate a more serious problem‚ such as a faulty motor winding or internal damage. In such cases‚ replacement is usually necessary. Always refer to the safety precautions before attempting any maintenance or repair procedures. If unsure about any aspect of troubleshooting or maintenance‚ consult a qualified technician.
Regular Maintenance Procedures for Optimal Performance
Regular maintenance of your M92 servo motor is crucial for ensuring its longevity and optimal performance. A key aspect of this is keeping the motor clean. Accumulated dust‚ debris‚ and other contaminants can interfere with its operation and lead to premature wear. Periodically inspect the motor for any visible dirt or grime. Use a soft brush or compressed air to carefully remove any loose particles. Avoid using harsh chemicals or solvents that could damage the motor’s components. For more stubborn contaminants‚ consider using a specialized electronics cleaner.
Another important maintenance task is lubricating the motor’s gears. Over time‚ the gears can experience wear and tear‚ leading to increased friction and noise. Apply a small amount of high-quality lubricant specifically designed for servo motors. Avoid excessive lubrication‚ as this can attract more contaminants. After applying the lubricant‚ gently operate the motor to distribute the lubricant evenly throughout the gear train. Regular lubrication will significantly extend the lifespan of the motor and maintain its smooth operation.
Finally‚ inspect the motor’s wiring and connections regularly. Loose connections can lead to intermittent operation or complete failure. Ensure all connections are secure and properly seated. Check for any signs of damage to the wiring‚ such as fraying or breaks. Repair or replace any damaged wiring immediately to prevent further problems. Following these simple maintenance steps will help maintain the M92 servo motor’s peak performance and extend its operational lifespan.
Safety Precautions and Regulations
Always read the instruction manual before operating the M92 servo motor. Ensure proper grounding and avoid loose connections. Never operate the motor near flammable materials. Use appropriate safety gear during installation and maintenance.
Essential Safety Guidelines for M92 Servo Motor Operation
Before commencing any operation with the M92 servo motor‚ ensure you have thoroughly reviewed and understood all safety instructions detailed in this manual. Failure to adhere to these guidelines may result in serious injury or equipment damage. Always disconnect power to the motor before undertaking any maintenance‚ installation‚ or inspection procedures. Never attempt to operate the motor if it exhibits any signs of damage or malfunction; immediately cease operation and contact technical support.
Proper grounding is crucial for safe operation. Ensure the motor is correctly grounded to prevent electrical shocks. The operating environment must be well-ventilated to prevent overheating. Maintain a safe distance from moving parts during operation. Never attempt to bypass or disable any safety features incorporated into the motor’s design. Use appropriate personal protective equipment (PPE)‚ including safety glasses and gloves‚ when handling the motor or performing maintenance. Regularly inspect the motor’s cables and connections for any signs of wear or damage‚ replacing them immediately if necessary.
Always follow the manufacturer’s recommended operating parameters and guidelines to ensure optimal performance and longevity. Avoid overloading the motor beyond its specified capacity to prevent damage. Ensure proper ventilation around the motor to prevent excessive heat buildup. Improper use may void warranties. In the event of an emergency or malfunction‚ immediately switch off the power supply and contact qualified personnel for assistance. Regular inspections and preventative maintenance are key to ensuring continued safe and efficient operation.