manual fork lift
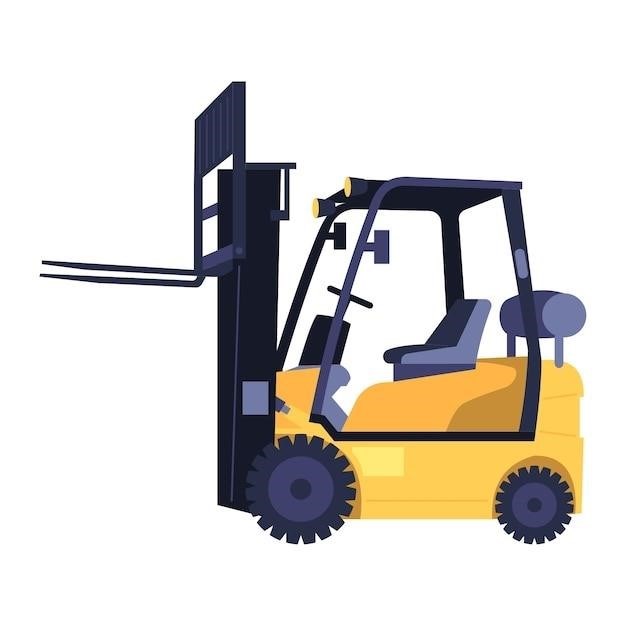
Manual Forklift Operation⁚ A Comprehensive Guide
This guide provides a comprehensive overview of safe manual forklift operation, covering pre-operational checks, load capacity understanding, safe driving procedures, terrain navigation, and proper load handling techniques; It emphasizes adherence to OSHA regulations and best practices for accident prevention and maintenance.
Pre-Operational Checklist and Safety Inspections
Before operating a manual forklift, a thorough pre-operational checklist is crucial for ensuring safe operation and preventing accidents. This checklist should include a visual inspection of the forklift’s tires for wear and tear, checking for any leaks (oil, gas, etc.), and verifying the functionality of all lights, the horn, and the seatbelt. The operator must confirm that all safety devices are in proper working order. The mast should be inspected for any damage or signs of wear, and the forks should be checked for straightness and secure attachment. Furthermore, the operator must ensure that the forklift’s load capacity is appropriate for the intended load and that the load is properly secured and balanced before attempting to lift or move it. This pre-operational inspection is not merely a formality; it is a critical step in preventing accidents and ensuring a safe working environment.
Understanding Load Capacity and Stability
Understanding a manual forklift’s load capacity and maintaining stability are paramount for safe operation. The forklift’s data plate clearly indicates its maximum load capacity, which should never be exceeded. Overloading can lead to instability, tipping, and serious accidents. Proper load distribution is equally critical. The load should be evenly distributed across the forks, ensuring its center of gravity is centered. Uneven loads significantly increase the risk of tipping, especially during turns or on uneven terrain. Before lifting, operators must visually assess the load’s stability and ensure it’s properly secured to prevent shifting during transport. Additionally, the operator must be aware of the forklift’s own stability, considering factors like the terrain, incline, and any potential obstacles. Consistent awareness of these factors contributes significantly to preventing accidents and ensuring safe operation.
Safe Operating Procedures⁚ Driving and Maneuvering
Safe operation of a manual forklift necessitates adherence to specific driving and maneuvering procedures. Always maintain a safe speed, adjusting it according to conditions such as terrain, visibility, and pedestrian traffic. Sudden acceleration or deceleration should be avoided, as should sharp turns, especially when carrying a load. Before making turns, operators should carefully assess the surrounding area for any potential obstacles or personnel. Smooth, controlled movements are essential to prevent accidents. When navigating tight spaces or confined areas, operators should proceed slowly and cautiously, utilizing mirrors and maintaining awareness of their surroundings. The use of appropriate hand signals when working with other personnel is crucial for communication and safety. Always ensure the load is stable and secure before driving, and avoid raising or lowering the load while in motion. Consistent vigilance and adherence to these procedures are key to preventing forklift-related incidents.
Navigating Different Environments and Terrain
Operating a manual forklift in diverse environments demands adaptability and caution. On uneven terrain, reduce speed significantly and avoid sudden movements to maintain stability and prevent tipping. When traversing ramps or inclines, proceed slowly and cautiously, ensuring the load is properly balanced and secured. Never exceed the forklift’s rated capacity, especially on inclines, as this dramatically increases the risk of an accident. In confined spaces like warehouses or loading docks, maneuver slowly and deliberately, using mirrors and maintaining awareness of surroundings to prevent collisions with obstacles or personnel. On wet or slippery surfaces, reduce speed considerably and avoid sharp turns to prevent loss of control. When operating outdoors, be mindful of weather conditions such as rain, snow, or ice, which can significantly reduce traction. Always adapt driving techniques to the specific environmental challenges presented, prioritizing safety above speed and efficiency.
Proper Load Handling Techniques
Safe and efficient load handling is paramount when operating a manual forklift. Before lifting, carefully assess the load’s weight and dimensions to ensure they do not exceed the forklift’s capacity. Center the load on the forks to maintain balance and stability throughout the operation. Ensure the load is properly secured to prevent shifting or falling during transport. Use appropriate lifting techniques to avoid sudden movements or jerky actions that could damage the load or the forklift. When stacking loads, maintain a stable base and avoid creating unstable formations. Always lower loads slowly and carefully to prevent damage or injury. When maneuvering with a load, maintain a safe distance from obstacles and personnel. Before setting down a load, ensure the area is clear and stable. Never attempt to lift or carry a load exceeding the forklift’s stated capacity. Regularly inspect the forks and load securing mechanisms for any damage or wear to ensure continued safe operation. Following these techniques minimizes risks and ensures efficient material handling.
OSHA Regulations and Compliance
Understanding and adhering to OSHA’s forklift safety regulations is crucial. This includes operator training, regular inspections, and reporting procedures for incidents and near misses to prevent accidents and ensure workplace safety.
Essential Training Requirements for Operators
OSHA mandates comprehensive training for all forklift operators. This training must include formal written instruction covering safety regulations, operating procedures, and pre-operational checks. Practical training is equally vital, allowing trainees to apply learned knowledge in a controlled environment under the supervision of a qualified instructor. This hands-on experience ensures operators develop the necessary skills to handle various situations and terrains safely. A skills evaluation, often involving a practical test, is essential to assess competency before operators are permitted to operate forklifts independently. The evaluation should cover aspects like pre-operational inspections, safe load handling, maneuvering techniques, and emergency procedures. Failure to complete all aspects of the training and pass the evaluation can lead to suspension of operating privileges. Refresher courses are often required periodically to maintain proficiency and stay updated on safety regulations and best practices.
Key Safety Rules and Guidelines to Follow
Prior to operating a forklift, always conduct a thorough pre-operational inspection, checking brakes, lights, horn, seatbelts, and overall vehicle condition. Never exceed the forklift’s rated load capacity; overloading significantly increases the risk of accidents. Maintain a safe speed, especially in congested areas or when navigating turns. Always wear a seatbelt when one is available, and ensure the load is stable and properly secured before moving. Avoid raising or lowering the load while traveling. Keep a safe distance from platform and ramp edges. When operating outdoors, ensure the mast and chains remain stable. Use appropriate hand signals when working with other personnel. Never operate a forklift if you are fatigued or under the influence of drugs or alcohol. Regularly check the operator’s manual for specific instructions and warnings. Report any mechanical issues or safety concerns immediately. Follow all company policies and procedures related to forklift operation. Remember that continuous training and awareness are crucial for safe operation and to prevent accidents.
Consequences of Non-Compliance and Accident Prevention
Failure to comply with OSHA regulations and safe operating procedures for manual forklifts can lead to severe consequences, including serious injuries or fatalities to operators and bystanders. Accidents involving forklifts frequently result from inadequate training, highlighting the critical need for comprehensive operator education. OSHA estimates thousands of serious injuries and numerous fatalities annually due to forklift accidents. Non-compliance can result in hefty fines and legal repercussions for employers. Beyond the human cost, accidents disrupt operations, leading to lost productivity, equipment damage, and increased insurance premiums. To prevent accidents, prioritize comprehensive training programs that cover all aspects of safe operation, regular maintenance schedules, and strict adherence to safety rules. Implement clear safety protocols and communication systems to facilitate safe working conditions. Regular inspections of forklifts and the work environment are crucial for identifying and mitigating potential hazards. Promote a strong safety culture where reporting near misses and incidents without fear of reprisal is encouraged. Remember, proactive safety measures are significantly more cost-effective than dealing with the aftermath of an accident.
Reporting Procedures for Incidents and Near Misses
Establishing a robust system for reporting forklift incidents and near misses is crucial for continuous improvement in workplace safety. All incidents, regardless of severity, should be documented thoroughly, including the date, time, location, individuals involved, a detailed description of the event, and any contributing factors; A standardized reporting form should be used to ensure consistency and completeness of information. The reporting process should be straightforward and accessible to all employees, encouraging open communication and minimizing barriers to reporting. Training should emphasize the importance of reporting, assuring employees that reporting near misses is not a disciplinary action, but a valuable tool for identifying potential hazards and preventing future incidents. Management should review all reports promptly and thoroughly to identify trends, implement corrective actions, and update safety procedures as needed. A system for tracking and analyzing reported incidents and near misses allows for identifying recurring problems, evaluating the effectiveness of safety interventions, and demonstrating a commitment to continuous improvement in workplace safety. Regular safety meetings should be conducted to discuss reported incidents and near misses, fostering a culture of safety awareness and shared responsibility.
Maintenance and Troubleshooting
Regular maintenance, including inspections and repairs, is vital for safe forklift operation. Addressing mechanical issues promptly prevents accidents and ensures optimal performance. Consult the operator’s manual for detailed maintenance schedules and procedures.
Regular Maintenance Schedules and Procedures
Establishing a regular maintenance schedule is crucial for ensuring the longevity and safe operation of your manual forklift. This involves more than just occasional spot checks; it requires a systematic approach to identifying and addressing potential issues before they escalate into costly repairs or, worse, accidents. A comprehensive schedule should include daily pre-operational inspections, covering components like tires, brakes, lights, horns, and fluid levels; Weekly checks should focus on more in-depth assessments, such as examining the mast for any signs of damage or wear, inspecting hydraulic systems for leaks, and lubricating moving parts. Monthly maintenance might involve more extensive tasks, such as changing filters, inspecting the battery (for electric forklifts), and checking the overall condition of the forklift’s chassis. Finally, annual maintenance should include a thorough professional inspection by a qualified technician to ensure the forklift remains compliant with safety regulations and operates at peak efficiency. Maintaining detailed records of all inspections and maintenance performed is essential for tracking the forklift’s history and ensuring compliance with safety standards. Remember, preventative maintenance is significantly more cost-effective than reactive repairs.
Identifying and Addressing Common Mechanical Issues
Proactive identification and resolution of mechanical issues are paramount for maintaining a safe and efficient manual forklift operation. Regular inspections, as outlined in the maintenance schedule, are the first line of defense. Common problems include hydraulic leaks, which can manifest as fluid drips or reduced lifting power; addressing this requires identifying the leak source and repairing or replacing damaged seals or components. Tire wear and damage are also frequent issues; worn tires compromise stability and handling, necessitating replacement or repair. Problems with the mast, such as bending or damage to rollers, can affect lifting capacity and stability; these require immediate attention from a qualified mechanic. Brake issues, such as reduced stopping power or inconsistent braking, are serious safety concerns and demand prompt professional evaluation and repair. Electrical problems in electric forklifts, including issues with the battery or motor, can significantly impact performance and safety; these often require specialized attention. Regular lubrication of moving parts is essential for smooth operation and preventing premature wear; neglecting lubrication can lead to increased friction, damage, and ultimately, failure. Any unusual noises, vibrations, or performance changes should be investigated immediately; ignoring such warning signs can lead to more serious problems down the line. Maintaining a detailed log of all mechanical issues encountered and their resolutions is vital for tracking trends and ensuring future maintenance effectiveness.