powerflex 753 manual pdf
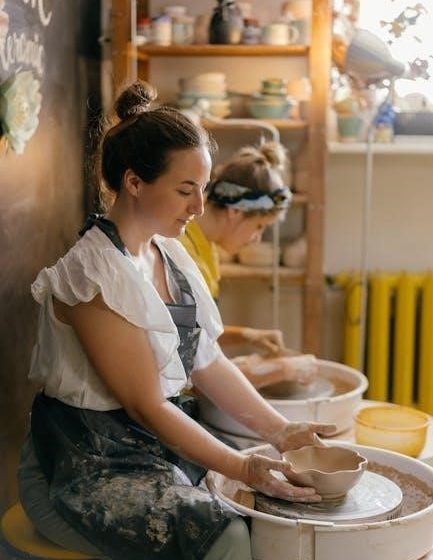
The PowerFlex 753 manual provides comprehensive guidance for installing, configuring, and troubleshooting the drive, ensuring optimal performance and compliance with industry standards.
Overview of the PowerFlex 753 Drive
The PowerFlex 753 drive, part of the PowerFlex 750 series, is a versatile and reliable variable frequency drive designed for a wide range of industrial applications. It offers advanced motor control capabilities, high performance, and seamless integration with Rockwell Automation’s ecosystem. The drive supports multiple control methods, including vector control and volts per hertz, ensuring precise motor operation. Its compact design and user-friendly interface make it ideal for applications requiring flexibility and efficiency. The PowerFlex 753 is widely used in industries such as manufacturing, material handling, and HVAC systems, providing robust solutions for motor speed control and automation needs.
Key Features of the PowerFlex 753 Series
The PowerFlex 753 series stands out with its advanced features, including high-performance motor control, flexible I/O options, and compatibility with Rockwell Automation’s software tools. It supports vector control for precise speed regulation and efficient energy use. The drive also offers integrated safety features, such as safe torque off, ensuring operational safety. With a robust design and user-friendly configuration, the PowerFlex 753 is ideal for demanding industrial applications. Its scalability and adaptability make it a reliable choice for meeting diverse automation needs while maintaining high performance and reliability.
Installation and Setup Guidelines
The PowerFlex 753 manual outlines essential steps for proper installation, including mounting, wiring, and configuration, ensuring safe and efficient setup for optimal drive performance.
Physical Installation of the PowerFlex 753
The PowerFlex 753 must be installed in a well-ventilated area, mounted on a sturdy base to ensure stability. Proper grounding is essential to prevent electrical hazards. The drive should be positioned away from direct sunlight and moisture to maintain optimal operating conditions. Follow the manual’s guidelines for securing the unit and ensuring all components are correctly aligned. Adhere to Rockwell Automation’s specifications for frame sizes and environmental considerations to guarantee reliable performance and longevity of the equipment.
Wiring and Electrical Connections
Proper wiring is critical for safe and efficient operation of the PowerFlex 753. Use the correct gauge and type of cable as specified in the manual to ensure reliable connections. All terminals must be securely tightened to prevent loose connections, which can cause faults. Follow the recommended wiring diagrams for power and control terminals, ensuring compliance with local electrical standards. Double-check all connections before applying power to avoid damage or safety risks. Refer to Rockwell Automation’s guidelines for specific wiring requirements and best practices to maintain system integrity and performance. Always ensure the drive is properly grounded to prevent electrical hazards.
Initial Setup and Configuration Steps
Begin by connecting the PowerFlex 753 to a PC using DriveExplorer or DriveExecutive software. Follow the manual’s guidelines to set up motor and drive parameters, ensuring accurate configuration. Connect the drive using a USB or Serial interface, then power up the unit. Use the software to configure motor nameplate data, speed references, and control modes. Review and save all settings before testing. Ensure all parameters align with your application requirements. Refer to Rockwell Automation’s setup guide for detailed instructions to avoid errors. Proper initialization ensures smooth operation and prevents potential issues. Always follow safety protocols during setup.
Configuration and Parameter Settings
Configure motor and drive parameters, including speed, torque, and control modes, to optimize performance for specific applications, ensuring precise control and operational efficiency.
Understanding Parameter Groups and Settings
The PowerFlex 753 manual details parameter groups, which organize settings for motor control, I/O, and advanced features. These groups simplify configuration by categorizing related parameters, ensuring efficient setup. Key parameters include motor nameplate data, speed and torque limits, and control modes. Customizable settings allow tailored performance for specific applications. The manual provides guidance on navigating and adjusting these parameters, enabling precise control and optimization of drive operation. Proper configuration ensures reliable performance, while incorrect settings may lead to operational issues. Referencing the manual is crucial for understanding each parameter’s function and ensuring optimal drive efficiency.
Configuring I/O and Control Interfaces
The PowerFlex 753 manual outlines steps for configuring I/O and control interfaces, enabling seamless integration with external devices. It covers digital and analog inputs/outputs, ensuring precise control signals. The manual provides wiring diagrams and setup instructions for interfaces like USB, Ethernet, and serial connections. Configuration tools such as DriveExplorer simplify parameter adjustments. Proper I/O setup ensures reliable communication between the drive and control systems, minimizing errors. Detailed troubleshooting guides help resolve connectivity issues, ensuring smooth operation. This section is essential for optimizing the drive’s interaction with external components and achieving desired performance levels in industrial applications.
Advanced Configuration Options for Custom Applications
The PowerFlex 753 manual details advanced configuration options for tailored applications, enabling customized control logic and specialized I/O setups. Users can leverage parameter customization, adaptive control algorithms, and programmable outputs to meet specific application demands. The manual also covers integrating the drive with external systems using tools like DriveExplorer. Advanced features such as custom start/stop logic and adaptive acceleration/deceleration profiles are explained, ensuring precise motor control. These options enhance the drive’s adaptability, allowing users to address unique operational requirements. Referencing the manual ensures optimal configuration for complex industrial automation needs.
Operation and Control Modes
The PowerFlex 753 supports multiple operation modes, including manual control, speed regulation, and integration with HMI systems, ensuring versatile and precise motor control for industrial applications.
Operating Modes of the PowerFlex 753
The PowerFlex 753 offers multiple operation modes, including Manual Mode for direct speed control, Speed Regulation Mode for precise velocity management, and Integrated Mode for seamless HMI system connectivity. These modes ensure flexibility in industrial applications, allowing users to adapt the drive to specific operational needs. The drive can be easily switched between modes using DriveExplorer or DriveExecutive software tools, enabling efficient configuration and monitoring. Additionally, advanced features like SCANport technology enhance communication and control capabilities, making the PowerFlex 753 a versatile solution for diverse motor control requirements.
Using Manual Control and Speed Settings
The PowerFlex 753 allows for precise manual control and speed adjustments, enabling operators to set motor speed directly. This mode is ideal for applications requiring immediate control without automation. Users can enable manual control via digital inputs or through DriveExecutive software. Speed settings can be adjusted using potentiometers or programmed parameters such as PR001 (min speed) and PR002 (max speed). The drive also supports manual acceleration and deceleration rates, configurable via PR003 and PR004. Ensure proper configuration by referring to the manual to avoid operational errors and optimize performance.
Integration with HMI and Control Systems
The PowerFlex 753 seamlessly integrates with HMI and control systems, enabling real-time monitoring and control. Using communication protocols like EtherNet/IP or DeviceNet, the drive connects to Rockwell Automation’s Integrated Architecture. DriveExplorer and DriveExecutive software tools facilitate parameter configuration and monitoring. HMIs can access drive status, speed, and fault codes through predefined tags. This integration enhances operational efficiency and centralized control, allowing for precise command execution and data exchange. Refer to the manual for detailed configuration steps and compatibility guidelines to ensure smooth system integration and optimal performance.
Diagnostics and Troubleshooting
The PowerFlex 753 manual details diagnostic tools and troubleshooting steps for resolving drive issues, including fault code identification and advanced software-based solutions for optimal maintenance.
Identifying Fault Codes and Alarms
The PowerFlex 753 manual outlines procedures for identifying and interpreting fault codes and alarms, enabling users to quickly diagnose and address drive issues. The TELEMETRY USER INTERFACE displays fault codes, while detailed troubleshooting steps guide users through resolving common problems. Specific fault codes, such as those related to overcurrent or overheating, are explained, along with recommended actions. Advanced diagnostic tools, like DriveExplorer and DriveExecutive, provide real-time monitoring and historical data analysis. The manual emphasizes systematic approaches to fault identification, ensuring efficient issue resolution and minimizing downtime in industrial applications. This section is essential for maintaining operational efficiency and system reliability.
Common Issues and Solutions
Common issues with the PowerFlex 753 include incorrect wiring, parameter misconfigurations, and overheating. Fault codes like “Overcurrent” or “Thermistor Fault” indicate specific problems. Solutions involve checking connections, resetting parameters, and ensuring proper cooling. The manual provides detailed troubleshooting steps, such as using DriveExplorer to monitor real-time data and diagnose faults. Regular maintenance, like updating firmware, can prevent recurring issues. Users should also refer to Rockwell Automation’s technical support resources for additional guidance. Addressing these common problems promptly ensures reliable operation and minimizes downtime in industrial applications. Properly resolving issues requires a systematic approach, as outlined in the manual.
Tools and Techniques for Effective Troubleshooting
Effective troubleshooting of the PowerFlex 753 requires tools like DriveExplorer and DriveExecutive for real-time monitoring and parameter adjustments. These software tools enable users to identify and resolve issues efficiently. Fault codes and alarm messages provide specific clues about system malfunctions, guiding targeted repairs. The manual also outlines step-by-step diagnostic procedures, including checking electrical connections and verifying parameter settings. Regularly reviewing the drive’s operational data and logs can help pinpoint recurring problems. By combining these tools and techniques, users can quickly identify and address issues, minimizing downtime and ensuring optimal performance. Proper use of these resources is essential for effective troubleshooting.
Maintenance and Support
The PowerFlex 753 manual outlines routine maintenance procedures, firmware upgrades, and access to Rockwell Automation’s technical support resources, ensuring long-term reliability and performance.
Routine Maintenance Procedures
Regular maintenance ensures optimal performance and longevity of the PowerFlex 753 drive. Clean the drive and its surroundings to prevent dust buildup, which can cause overheating. Check all electrical connections for tightness and integrity. Inspect fans and heat sinks for proper airflow and cleanliness. Update firmware periodically to access new features and improvements. Refer to the manual for detailed schedules and procedures to ensure compliance with Rockwell Automation’s recommendations.
Adhere to safety guidelines during maintenance, such as disconnecting power before servicing. The manual provides step-by-step instructions for routine checks and repairs, ensuring reliable operation and minimizing downtime.
Upgrading Firmware and Software
Upgrading the PowerFlex 753 firmware and software ensures access to new features, improved performance, and compatibility with the latest Rockwell Automation systems. Always download updates from Rockwell Automation’s official website to ensure authenticity and security. Before starting, backup your configuration to prevent data loss. The manual provides detailed steps for a smooth upgrade process, including pre-upgrade checks and post-upgrade verification. Follow the instructions carefully to avoid errors and maintain system stability. Regular firmware updates are crucial for optimal drive functionality and integration with other Rockwell Automation products.
Accessing Technical Support and Resources
For assistance with the PowerFlex 753, Rockwell Automation offers extensive technical support and resources.Visit their official website for manuals, troubleshooting guides, and FAQs.Additionally, users can contact Rockwell Automation’s support team directly via phone or email for personalized assistance.The website also provides access to software tools like DriveExplorer and DriveExecutive, which simplify configuration and monitoring.Engage with online forums and communities for peer-to-peer support and expert advice.Ensure you have the latest updates by registering for a Rockwell Automation account, granting access to exclusive resources and priority support;
Safety Guidelines and Compliance
Adhere to safety standards and regulations when handling the PowerFlex 753. Follow proper installation, operation, and maintenance procedures to ensure compliance and prevent hazards.
Safety Precautions for Installation and Operation
Ensure all safety measures are followed during installation and operation of the PowerFlex 753. Always disconnect power before performing maintenance. Wear protective gear, including gloves and safety glasses, to prevent injury. Avoid overloading the system, as this can lead to equipment failure or electrical hazards. Properly ground the drive to prevent electrical shocks. Follow all industry standards and manufacturer guidelines to ensure safe and reliable operation. Regularly inspect components for wear or damage. Never operate the drive in environments with hazardous materials without proper protection. Failure to comply may result in serious harm or equipment damage.
Compliance with Industry Standards and Regulations
The PowerFlex 753 drive is designed to meet global industry standards, ensuring reliable and safe operation across various applications. It adheres to UL, CE, and RoHS certifications, guaranteeing compliance with electrical and environmental regulations. The drive is part of Rockwell Automation’s Integrated Architecture, aligning with industrial automation standards. Compliance ensures seamless integration with existing systems while meeting regulatory requirements. This adherence to standards also supports energy efficiency and reduces environmental impact. Always verify local regulations and ensure the drive is configured to meet specific regional standards for optimal performance and legal compliance.
Integration with Rockwell Automation Ecosystem
The PowerFlex 753 seamlessly integrates with Rockwell Automation’s ecosystem, offering compatibility with DriveExplorer and DriveExecutive software, enhancing automation capabilities and ensuring smooth system operation.
Using DriveExplorer and DriveExecutive Software
DriveExplorer and DriveExecutive software tools enhance the functionality of the PowerFlex 753, enabling advanced configuration, monitoring, and control. DriveExplorer simplifies parameter setup and real-time monitoring, while DriveExecutive provides scalable control for integrated systems. These tools offer intuitive interfaces for optimizing drive performance, ensuring seamless integration with Rockwell Automation’s ecosystem. They support efficient troubleshooting and customization, making them essential for maximizing the capabilities of the PowerFlex 753 in industrial automation applications.
Compatibility with Rockwell Software and Hardware
The PowerFlex 753 seamlessly integrates with Rockwell Automation’s software and hardware ecosystem, ensuring enhanced functionality and compatibility. It supports Rockwell’s Integrated Architecture, enabling effortless communication with ControlLogix, CompactLogix, and other Allen-Bradley controllers; The drive is also fully compatible with Rockwell’s FactoryTalk software suite, allowing for unified monitoring and control. This compatibility ensures a cohesive automation environment, simplifying system design and operation while maximizing performance and scalability.
Frequently Asked Questions
Common queries include installation steps, troubleshooting fault codes, and configuring I/O interfaces. Users also ask about compatibility with Rockwell software and optimal maintenance practices.
Common Queries About the PowerFlex 753
Users often inquire about installation steps, troubleshooting common fault codes, and configuring I/O interfaces. Questions also arise regarding compatibility with Rockwell Automation software and hardware. Many seek clarification on parameter settings, such as speed reference and motor control. Additionally, there are frequent queries about firmware upgrades, manual control modes, and integrating the drive with HMI systems. Some users ask about routine maintenance and diagnostic tools. Understanding these aspects ensures smooth operation and effective troubleshooting of the PowerFlex 753 drive.
Clarifications on Installation and Configuration
Common questions include proper grounding techniques and terminal connections to ensure safe and reliable operation. Users often seek clarity on parameter settings, such as motor nameplate data and speed references. Configuration of I/O interfaces, like enabling digital inputs for manual control, is another frequent topic. Additionally, many inquire about firmware compatibility and upgrade processes. Clarifications also cover troubleshooting installation issues, such as incorrect wiring or failed parameter downloads. Understanding these aspects is crucial for a smooth setup and optimal performance of the PowerFlex 753 drive. Always refer to the manual for detailed step-by-step guidance.
The PowerFlex 753 manual serves as an essential guide for optimizing drive performance, troubleshooting, and maintaining compliance with industry standards. It provides detailed instructions for installation, configuration, and advanced customization, ensuring seamless integration with Rockwell Automation’s ecosystem. By following the manual’s guidelines, users can maximize the drive’s efficiency and reliability. For further assistance, Rockwell Automation offers comprehensive technical support and resources, making the PowerFlex 753 a versatile and dependable solution for industrial applications. Refer to the manual regularly to ensure optimal operation and adherence to safety protocols.